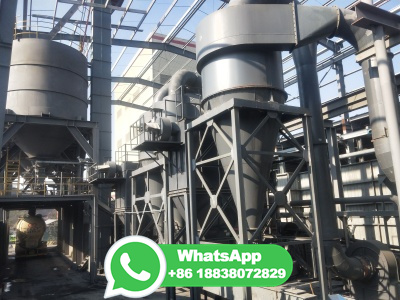
Iron ore production South Africa 2021
Mar 07, 2022 · In 2021, South Africa's production of iron ore amounted to an estimated 61 million metric tons. South Africa is one of the world's largest producers of iron ore. As of 2021, South Africa was the ...