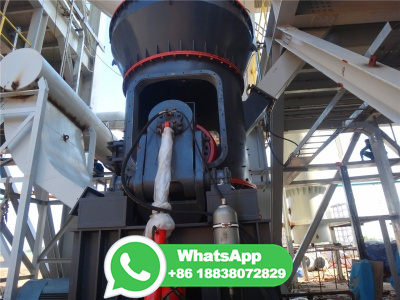
Top 5 productspecific milling technologies used in ...
Jul 07, 2017 · The four basic techniques used in size reduction of dry powders are impact, shear, attrition and compression forces. In some cases, a combination of these may be found in a single mill type. Impact and attrition sizereduction methods include air classifying mills, pin mills, hammer mills and jet mills.