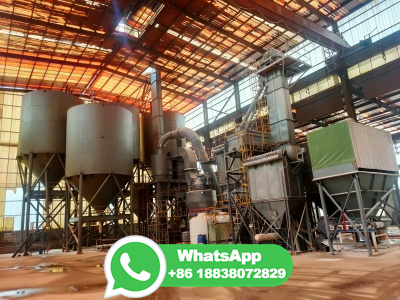
Machining
Machining is a term used to describe a variety of material removal processes in which a cutting tool removes unwanted material from a workpiece to produce the desired shape. The workpiece is typically cut from a larger piece of stock, which is available in a variety of standard shapes, such as flat sheets, solid bars, hollow tubes, and shaped beams.