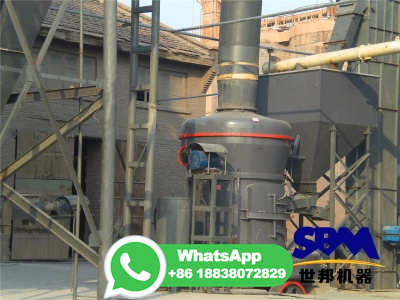
Rolling Mills: 6 Different Types of Rolling Mills [Images ...
· In the rolling process, the job is drawn through a set of rolls due to interface friction, and the compressive forces reduce the thickness of the workpiece or change in its crosssectional area.. The types of rolls used in rolling mills are depended upon the shape, size and the gap between the rolls and their contour. Because of workability and limitations in equipment, rolling .