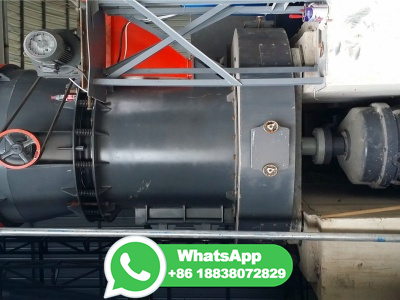
POP 7 : Aggregate Operations Planning — ASCM Monterrey
POP 7 : Aggregate Operations Planning — ASCM Monterrey. Why train with ASCM Why train with ASCM Monterrey CPIM Responsibilities Benefits Certifiions CLTD CPIM CSCP CPSM DDP PMP Principle Courses GREEN BELT Calendar Our Office Contact Us ASCM International Membership Course Enrollment About About ASCM Workshops Sales and Operations ...