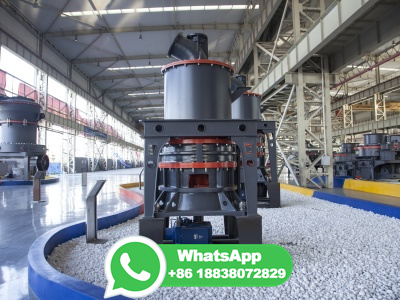
Ironmaking 101 – From Ore to Iron with Blast Furnaces ...
Oct 10, 2017 · Iron is made by reacting iron ore (iron oxide and impurities), coke (a reductant) and limestone (CaCO 3) in a blast furnace. Iron ores with lower iron content such as taconite are first processed to concentrate the iron level and drive off volatile impurities. The iron ore is dressed or crushed into in. chunks, which increases surface ...